Direct Injection Process (DIP) technology is a method used in the shoe manufacturing industry to produce high-quality, durable, and comfortable shoes.
In DIP, the liquid sole material (polyurethane material) is directly injected into a mold, creating a shoe sole that is strong, lightweight, and flexible. This technology offers several advantages over traditional shoe-making methods, including improved durability, comfort, and eco-friendliness.
DIP technology is commonly used to make athletic, casual, and children’s shoes, and has become an increasingly popular choice for shoe manufacturers.
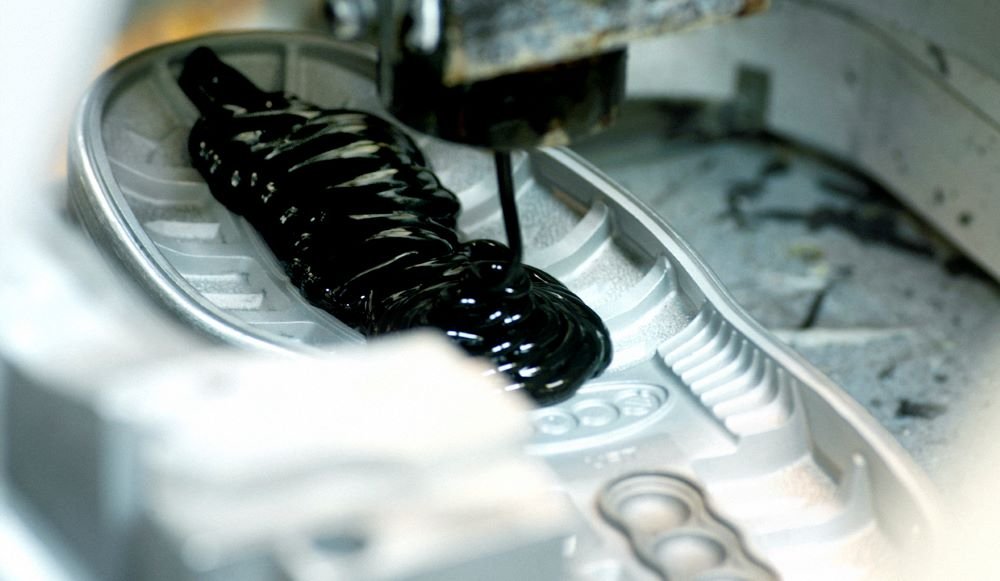
I. The benefits of DIP technology in making kids’ shoes
A. Durability
DIP technology enhances the durability of kids’ shoes by creating a strong and flexible sole that can withstand the wear and tear of daily activities.
In DIP, the PU material is directly injected into the heel of the mold, creating a one-piece sole that is seamlessly attached to the upper part of the shoe.
This eliminates the use of glue or stitching, which are common points of failure in traditional shoe-making methods.
The seamless design also helps prevent water and dirt from entering the shoe, which can cause wear and tear.
Additionally, the PU material used in DIP is highly resistant to abrasions and impact, which makes it ideal for child shoes that are subject to frequent use and rough treatment.
The result is a shoe that is more durable and long-lasting, making it a better value for families who want to buy shoes that will last.

B. Comfort
DIP technology enhances the comfort of kids’ shoes by creating a lightweight and flexible sole that conforms to the shape of the child’s foot.
In DIP, the PU material used is injected in a liquid form, which allows it to conform to the mold and create a sole that is custom-fitted to the shoe.
This results in a shoe that is more comfortable to wear and provides a safe and better fit, as it moves and flexes with the child’s foot.
The seamless design of the sole also eliminates potential pressure points and rubbing, which can cause discomfort.
Additionally, the PU material used in DIP is highly shock-absorbing, reducing the impact of each step on the children’s feet, legs, knees, and back.
The result is a shoe that is not only comfortable to wear but also helps promote good posture and healthy movement patterns.

Comparison with traditional shoe-making methods
Traditional shoe-making methods, such as stitching and gluing, often result in shoes that are less comfortable and durable than shoes made with DIP tech.
In traditional methods, the sole is often separate from the upper part of the shoe and is attached using glue or stitching.
This results in walking in a shoe that is heavier and less flexible, as the sole is not able to conform to the shape of the foot.
Additionally, the stitching and glue can cause pressure points and rubbing, which can lead to discomfort and blisters.
Traditional methods also result in a shoe that is less durable, as the glue and stitching can break down over time and cause the sole to separate from the upper.
In contrast, shoes made with DIP technology are lighter, more flexible, and more comfortable, as the one-piece sole is seamlessly attached to the upper and conforms to the shape of the foot.
The PU material used in DIP is also highly shock-absorbing and resistant to wear and tear, making the shoes more durable and long-lasting.
The use of DIP in kids’ shoe production results in a better overall product that is better suited to the needs of growing feet.

C. Eco-Friendliness
Firstly,
DIP technology reduces waste and pollution during production by eliminating the need for adhesives and other chemicals that are commonly used in traditional shoe-making methods.
In DIP, the PU material is directly injected into the mold, eliminating the need for glue and other chemicals that can release harmful fumes during production.
This not only reduces the amount of waste generated during production but also helps to improve air quality in the factory and surrounding areas.

Secondly,
DIP technology is a highly efficient production process that minimizes waste by reducing the number of steps involved in the production process.
This results in a more streamlined and efficient production process that reduces the overall carbon footprint of the manufacturing process.
The use of DIP in kids’ shoe production results in a product that is not only comfortable and durable but also environmentally friendly.
Additionally,
the PU material used in DIP is a type of hydrolysis-resistant material, which also can be recycled, making it easier to dispose of and reducing the environmental impact of the production process.
The result is a production process that is not only efficient and waste-free but also environmentally sustainable, making it a better choice for families who are concerned about the environment and the impact of their purchasing choices.
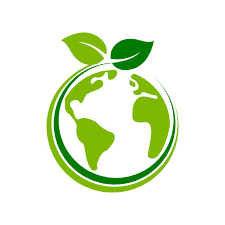
Finally,
The use of DIP technology in kids’ shoe production results in a product that is durable and long-lasting, reducing the need for frequent replacements and reducing waste in the long term.
This not only helps to promote sustainability but also makes it a more cost-effective choice for families.

II. How DIP technology improves the overall quality of kids’ shoes
A. Consistency
The Direct Injection Process (DIP) technology ensures consistency in the quality of kids’ shoes by controlling the production process from start to finish.
In DIP, the polyurethane (PU) material is directly injected into the mold in liquid form, allowing it to conform to the shape of the shoe and create a custom-fitted sole that is lightweight and flexible.
This eliminates the need for manual assembly and reduces the number of steps involved in the production process, which helps to ensure that every shoe is made to the same high standards.
Additionally, the use of PU in DIP technology results in a uniform and consistent material that is not subject to variations in quality.
This helps to ensure that every pair of kids’ shoes made with DIP is of the same high quality, providing parents with a reliable and consistent product.
The use of automated production processes also helps to minimize human error, reducing the chance of inconsistencies in quality and ensuring that every pair of kids’ shoes is made to the same high standards.
This helps to ensure that parents can rely on DIP technology to provide them with consistent and high-quality products for their children.
In conclusion, the use of DIP technology in kids’ shoe production ensures consistency in the quality of the final product, by controlling the production process, using a uniform and consistent material, and minimizing human error.
This provides parents with a reliable and consistent product that they can trust to provide the durability, comfort, and quality that their children need.

B. Better fit
- Conforms to the shape of the foot.
The Direct Injection Process (DIP) technology enhances the fit of kids’ shoes by creating a soft, custom-fitted sole that conforms to the shape of the foot.
In DIP, the polyurethane (PU) material is directly injected into the mold in liquid form, which allows it to conform to the shape of the shoe and create light and flexible soles.
This provides a more comfortable and supportive fit than traditional shoes, which can often be too loose or too tight and restrict the natural movement of the foot.
- Fit for growing feet.
The custom-fitted sole provided by DIP technology is especially important for growing feet.
As children grow and their feet change shape, it is important to provide them with shoes that are comfortable and supportive, as well as flexible enough to allow their feet and toes to move naturally.
This helps to promote good foot health and prevent foot problems, such as blisters and calluses, that can arise from wearing poorly fitting shoes.
- Reducing the risk of blisters and other foot problems
In addition, the use of PU in DIP technology helps to reduce friction between the foot and the sole of the shoe, reducing the risk of blisters and other foot problems.
This provides children with a comfortable and supportive shoe that allows their feet to grow and develop naturally, promoting good foot health at different age and stage.
In conclusion, the use of DIP in kids’ shoe production enhances the fit of the final product, providing a custom-fitted sole that conforms to the shape of the foot.
This is especially important for growing feet, helping to protect children`s feet and prevent foot problems while providing a comfortable and supportive fit.

III. Examples of DIP technology in kids’ shoe production
There are several well-known and respected brands that use Direct Injection Process (DIP) technology to manufacture kids’ shoes. Some of these brands include:
ECCO
Ecco – A Danish brand that is known for its high-quality footwear and innovative technology, Ecco uses DIP technology to create comfortable and durable shoes for children.
SUPERFIT
Superfit – An Austrian brand that is committed to providing children with shoes that are comfortable, supportive, and healthy, Superfit uses DIP technology to create custom-fitted sneakers for kids.
ELEFANTEN
Elefanten – A German brand that has been making shoes for children for over 100 years, Elefanten uses DIP technology to create shoes that are comfortable, supportive, and of the highest quality.
RICHTER
Richter – A German brand that is dedicated to making shoes for kids that are healthy and comfortable, Richter uses DIP technology to create shoes that are custom-fitted and supportive.
REIMA
Reima – A Finnish brand that is known for its high-quality and innovative clothing and footwear, Reima uses DIP technology to create shoes that are comfortable and supportive for kids.
These brands are all known for their commitment to providing children with shoes that are comfortable, supportive, and of the highest quality, and they all use DIP technology to help achieve these goals.
Whether you are looking for shoes for your child or simply interested in the latest advances in footwear technology, these brands are well worth considering.
Conclusion
In conclusion, Direct Injection Process (DIP) technology offers several advantages when it comes to making kids’ shoes. From enhancing the durability and comfort of the shoes to reducing waste and pollution during production, DIP technology provides a number of benefits that make it an excellent choice for children’s footwear.
DIP technology also ensures consistency in the quality of the final product, providing a custom-fitted sole that conforms to the shape of the foot. This is especially important for growing feet, as it helps to promote good foot health and prevent foot problems.
Brands such as Ecco, Superfit, Elefanten, Richter, and Reima are just a few of the many well-known and respected brands that use DIP technology to manufacture kids’ shoes.
These brands are all dedicated to providing children with shoes that are comfortable, supportive, and of the highest quality, and they use DIP technology to help achieve these goals.
In final thoughts, the use of DIP technology in kids’ shoes is a great step forward in the world of footwear, offering numerous benefits to both children and the environment.
Whether you are a parent looking for the best shoes for your child, or a footwear manufacturer looking to incorporate the latest technology into your products, DIP technology is definitely worth considering.
